A commitment to high standard and productivity
Our aluminum alloy welding wires, magnesium alloy welding wires, and light alloy 3D printing wires such as 2024, 7050, 5-series aluminum alloy with scandium all meet or exceed international standards.
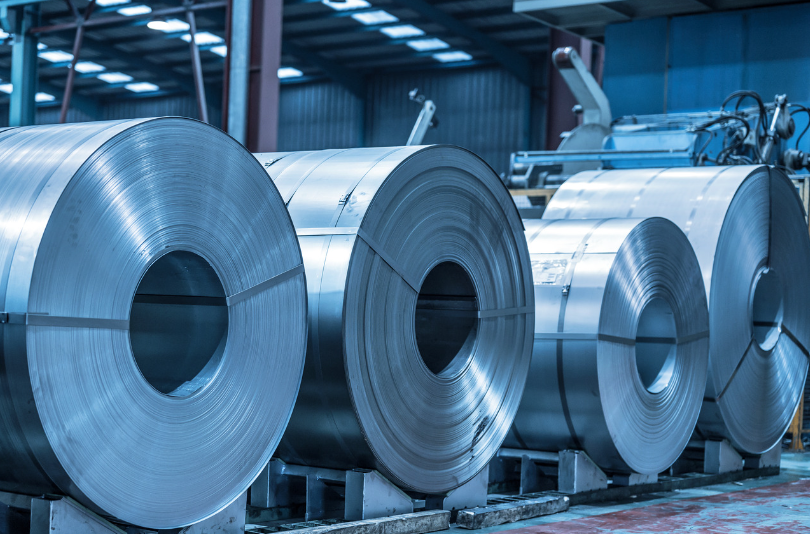
Aluminum Alloy Welding Wires
2319
- Offers higher strength and better ductility when used for welding 2 series aluminum alloys.
- Provides excellent resistance to stress-corrosion cracking when high-temperature performance is required
Si | Fe | Cu | Mn | Mg | Zn | Ca. Y | Ti | Be |
≤0.20 | ≤0.30 | 5.80~6.80 | 0.20~0.40 | ≤0.02 | ≤0.10 | 0.05~0.15 | 0.10~0.20 | ≤0.0003 |
Si | Fe | Cu | Mn | Mg | Zn | Ti | Be |
4.50~6.00 | ≤0.80 | ≤0.30 | ≤0.05 | ≤0.05 | ≤0.10 | ≤0.20 | ≤0.0003 |
4043
- Lower melting point and better fluidity than 5 series aluminum alloys.
- Squeezed and cast parts have a more aesthetic weld seam surface, and welded parts can be heat treated.
- Not recommended for use in anodizing conditions.
5356
- The most widely used aluminum alloy welding material.
Si | Fe | Cu | Mn | Mg | Cr | Zn | Ti |
≤0.25 | ≤0.40 | 0.10 | 0.05~0.20 | 4.50~5.50 | 0.05~0.20 | ≤0.10 | 0.06~0.20 |
Si | Fe | Cu | Mn | Mg | Cr | Zn | Ti | Zr | Be |
≤0.25 | ≤0.40 | ≤0.05 | 0.70~1.10 | 4.50~5.20 | 0.05~0.25 | ≤0.25 | ≤0.15 | 0.10~0.20 | ≤0.003 |
5087
- Designed to meet higher strength and corrosion resistance.
- It can refine the microstructure of the weld metal and reduce the tendency for hot cracking in the weld.
Magnesium Alloy Welding Wire
Our magnesium alloy coiled wire features a smooth surface similar to aluminum welding wire, offering excellent wire feeding performance. Besides listed products, Hyprus also provides rare earth magnesium alloy welding wires required for military applications.
AZ31B
Al | Zn | Cu | Mn | Mg | Zn | Ca. Y | Ti | Be |
≤0.20 | ≤0.30 | 5.80~6.80 | 0.20~0.40 | ≤0.02 | ≤0.10 | 0.05~0.15 | 0.10~0.20 | ≤0.0003 |
AZ91
Al | Zn | Mn | Si | Fe | Cu | Ni |
8.50~9.50 | 0.45~0.90 | 0.17~0.40 | ≤0.08 | ≤0.004 | ≤0.02 | 0.001 |
AZ61
Al | Zn | Mn | Si | Fe | Cu | Ni |
5.80~7.20 | 0.40~1.50 | 0.15~0.50 | ≤0.10 | ≤0.005 | ≤0.05 | ≤0.005 |
“Welding Productivity, Welding the Future.”
Jianghai You
CEO, Hyprus